top of page
Bower Engineering Solutions I Tel: 01955 601 212 I Email: info@berk-eng.com
Bower Engineering Solutions - ( A Division of Berkshire Engineering Supplies Ltd )

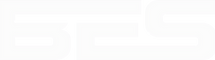

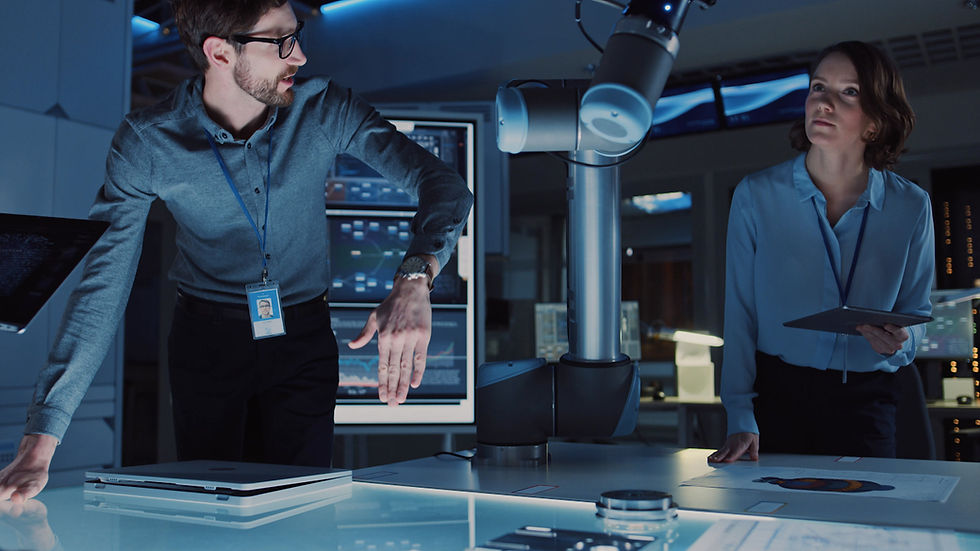
Bower Engineering Solutions I Tel: 01955 601 212 I Email: info@berk-eng.com
Bower Engineering Solutions - ( A Division of Berkshire Engineering Supplies Ltd )
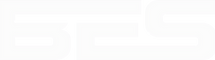
Our Projects
Delivering Engineering Excellence for every Project.
Bower Engineering Solutions
Engineering Excellence for Sustainable Solutions
Bower Engineering Solutions (BES) is dedicated to delivering sustainable engineering solutions that stand the test of time. Our team is committed to creating innovative and enduring projects tailored to meet the unique needs of the Nuclear Decommissioning, Renewable Energy, and Construction industries. We invite you to explore our expertise and discover how we can contribute to your next endeavour.

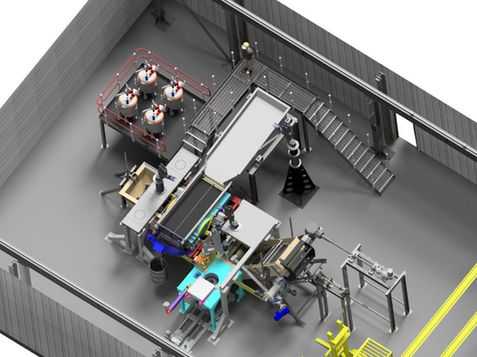
NRS Dounreay – Shaft and Silo Process Cell Prototyping.
The Dounreay Shaft is an historic radioactive waste disposal facility excavated in solid rock within the boundary of the Dounreay site. One essential part of the original site facilities was a means of disposal of low-level liquid waste through sea discharge pipes. To house this pipeline a tunnel was constructed which extended approximately 600m offshore to a diffuser chamber. As a means of removing the excavated spoil, a vertical shaft, 4.6m in diameter, was excavated to a depth of 65m. Then a short 30m long connecting tunnel was driven from the bottom of the shaft to intercept the discharge pipeline tunnel. When construction of the tunnel was complete, the shaft became redundant, and approval was granted in 1957 to use it as a disposal facility for radioactive waste. The shaft was isolated from the tunnel complex via the construction of a reinforced concrete plug in the connecting tunnel. Between 1959 and 1971, over 10,000 disposals of intermediate level radioactive waste were made to the shaft. In 1971, the availability of a new wet silo for the disposal of both sludge and solid intermediate level waste reduced further usage of the shaft to the disposal of items too large for the new silo.
In integral part of the works at NRS Dounreay site is the retrieval, processing, and packaging of waste from the shaft and silo in order to render it suitable for long-term storage and future disposal. To this end, new facilities and equipment is required to facilitate the decommissioning programme of Shaft and Silo.
The waste treatment process is to retrieve waste from the Shaft and Silo and undertake various waste sorting, segregation, and packaging operations. These operations will be undertaken within the Shaft and Silo Process Cell which is currently at Scheme Design Level.
Utilising Bower Engineering Services’ in-house Prototyping Design and Manufacture Procedure we have been instrumental in the design development and de-risking of the Process Cell equipment.
Works have included:
• Requirements capture and revision
• Optioneering
• Design for manufacture
• Scheme design development
• Detailed design
• Design across mechanical, process, electrical, control and instrumentation disciplines
• In-house manufacture and assembly
• Production of Prototype Testing Test Definition Documents and Test Schedules
• Extensive in-house isolated and integrated Prototype testing of the equipment
• Iterative feedback of results from Prototype testing to the design team, before entering a controlled modifications, rework and retesting loop for iterative improvements to the design
• Production of Test Reports, design updates, as-built drawings, and more as further deliverables to the project
Type of Equipment Design and Manufactured in-house:
• Vibrating screens and conveying systems
• Lamella settling and greywater filtration systems
• Sludge screening, settling and screw conveying systems
• Mixing and dosing tanks
• In-drum annular mixing systems
Leveraging or rapid prototyping techniques, we have helped to significantly de-risk the design, provide certainty, increase technical readiness of the equipment, and ultimately reduce lead times and development costs for our client.
In integral part of the works at NRS Dounreay site is the retrieval, processing, and packaging of waste from the shaft and silo in order to render it suitable for long-term storage and future disposal. To this end, new facilities and equipment is required to facilitate the decommissioning programme of Shaft and Silo.
The waste treatment process is to retrieve waste from the Shaft and Silo and undertake various waste sorting, segregation, and packaging operations. These operations will be undertaken within the Shaft and Silo Process Cell which is currently at Scheme Design Level.
Utilising Bower Engineering Services’ in-house Prototyping Design and Manufacture Procedure we have been instrumental in the design development and de-risking of the Process Cell equipment.
Works have included:
• Requirements capture and revision
• Optioneering
• Design for manufacture
• Scheme design development
• Detailed design
• Design across mechanical, process, electrical, control and instrumentation disciplines
• In-house manufacture and assembly
• Production of Prototype Testing Test Definition Documents and Test Schedules
• Extensive in-house isolated and integrated Prototype testing of the equipment
• Iterative feedback of results from Prototype testing to the design team, before entering a controlled modifications, rework and retesting loop for iterative improvements to the design
• Production of Test Reports, design updates, as-built drawings, and more as further deliverables to the project
Type of Equipment Design and Manufactured in-house:
• Vibrating screens and conveying systems
• Lamella settling and greywater filtration systems
• Sludge screening, settling and screw conveying systems
• Mixing and dosing tanks
• In-drum annular mixing systems
Leveraging or rapid prototyping techniques, we have helped to significantly de-risk the design, provide certainty, increase technical readiness of the equipment, and ultimately reduce lead times and development costs for our client.

NRS Dounreay - Remote Handling Trials
As part of a requirement to provide certainty and de-risk a fully remote handled in-cell sorting, segregating and size reduction process, Bower Engineering Solutions produced a full-scale, off-site prototype rig in order to conduct various trials and testing of the proposed equipment.
Works included:
• Cost-effectively replicating proposed in-cell equipment to produce the full-scale prototype rig
• Collaboration with Brokk UK to set up and commission 2 Brokk 400’s and associated tooling for testing
• Installation of vision systems, remote control systems and a dedicated control room to replicate the on-site control arrangements
• Production of Test Definition Documentation as well as Test Reports and associated Video Footage and Photographs of testing
Works included:
• Cost-effectively replicating proposed in-cell equipment to produce the full-scale prototype rig
• Collaboration with Brokk UK to set up and commission 2 Brokk 400’s and associated tooling for testing
• Installation of vision systems, remote control systems and a dedicated control room to replicate the on-site control arrangements
• Production of Test Definition Documentation as well as Test Reports and associated Video Footage and Photographs of testing

Hinkley Point C
BES supplied two specifically designed concrete batching plants for producing sprayed concrete for the initial ground works and infrastructure in preparation for the installation of the new Nuclear Power Station at Hinkley Point C.
The two plants shared 2x 100t silos, however each plant was required to operate autonomously, therefore there were 8 aggregate bins (4 per plant), 2x radial conveyors and feed hoppers, 1x aggregate and watering heating system, 2x feed conveyors, 2x mixing towers complete with 2.25m3 twin shaft mixers, agitated micro-silica storage system, 4x insulated additive storage tanks, 2x 50t water tanks, 2x steel fibre dosing systems, and 2x dedicated control systems.
Works included:
• Bespoke design and configuration of plant items
• Procurement, supply, on-site installation and commissioning of plant equipment on a Nuclear Licensed Site
• Coordination of multiple stakeholders and subcontractors to achieve a successful installation
The two plants shared 2x 100t silos, however each plant was required to operate autonomously, therefore there were 8 aggregate bins (4 per plant), 2x radial conveyors and feed hoppers, 1x aggregate and watering heating system, 2x feed conveyors, 2x mixing towers complete with 2.25m3 twin shaft mixers, agitated micro-silica storage system, 4x insulated additive storage tanks, 2x 50t water tanks, 2x steel fibre dosing systems, and 2x dedicated control systems.
Works included:
• Bespoke design and configuration of plant items
• Procurement, supply, on-site installation and commissioning of plant equipment on a Nuclear Licensed Site
• Coordination of multiple stakeholders and subcontractors to achieve a successful installation

NRS Dounreay – Filter Change Structural Containment
The current Filter Change Robot was installed and commissioned in the late 1980s. The Filter Change Robot is a key piece of plant equipment, as it required to remotely replace spent Ventilation High Efficiency Particle Air (HEPA) Filters. The robot is now beyond its useful life and consequently requires replacing to permit continued filter change operations; which is a key decommissioning enabler for the client.
In order to facilitate removal of the defective Filter Change Robot and installation of the replacement Robot, a new temporary high-integrity structural containment facility is required to extend the working area of the Cell.
The key requirements for the structural containment are as follows.
• Ability to withstand 1500Pa ventilation depression.
• Incorporate internal lifting and pulling points
• Modular in nature to allow potential future reuse on other site decommissioning projects.
• Removable roof hatches.
• Airlock with equalisation valves to permit personnel access/egress.
• Doors to isolate the containment from the Cell environment.
• Ventilation dampers, filters and pressure relief valves.
• Required to fit within the very restricted space envelope within the facility.
Our scope was to take the concept/scheme design information supplied by our client and undertake the detailed design, manufacture & offsite testing of the structural containment. Works have included:
• Undertaking detailed design (mechanical & EC&I)
System requirements capture and validation
Calculations
3D model
Site surveys
Fully detailed fabrication drawings,
Manufacturing specification
Installation sequence diagrams
Outline installation method statement
Factory acceptance test schedule
Interface schedule
Staged design reviews
• In-house manufacture and assembly of the containment at our dedicated stainless-steel workshop at Bower. Manufacture undertaken in accordance with our stringent quality management systems and procedures.
• Undertake Factory Acceptance Testing of the containment according to a rigorous testing schedule.
• Package and delivery of the containment to the client site, ready for others to install.
In order to facilitate removal of the defective Filter Change Robot and installation of the replacement Robot, a new temporary high-integrity structural containment facility is required to extend the working area of the Cell.
The key requirements for the structural containment are as follows.
• Ability to withstand 1500Pa ventilation depression.
• Incorporate internal lifting and pulling points
• Modular in nature to allow potential future reuse on other site decommissioning projects.
• Removable roof hatches.
• Airlock with equalisation valves to permit personnel access/egress.
• Doors to isolate the containment from the Cell environment.
• Ventilation dampers, filters and pressure relief valves.
• Required to fit within the very restricted space envelope within the facility.
Our scope was to take the concept/scheme design information supplied by our client and undertake the detailed design, manufacture & offsite testing of the structural containment. Works have included:
• Undertaking detailed design (mechanical & EC&I)
System requirements capture and validation
Calculations
3D model
Site surveys
Fully detailed fabrication drawings,
Manufacturing specification
Installation sequence diagrams
Outline installation method statement
Factory acceptance test schedule
Interface schedule
Staged design reviews
• In-house manufacture and assembly of the containment at our dedicated stainless-steel workshop at Bower. Manufacture undertaken in accordance with our stringent quality management systems and procedures.
• Undertake Factory Acceptance Testing of the containment according to a rigorous testing schedule.
• Package and delivery of the containment to the client site, ready for others to install.

HS2
BES successfully designed, manufactured, installed, and commissioned three bespoke concrete batching plants, along with a concrete and water recycling system, for the Chiltern Tunnel section of the HS2 high-speed railway project.
Working closely with project engineers, BES developed a dedicated twin-mixer concrete batching plant to supply two on-site precast tunnel segment factories. These factories produce high-performance steel-fiber-reinforced concrete (SFRC) segments, integral to the tunnel’s structure. With a total of 112,000 wall segments required, precision and consistency were paramount.
The two tunnel segment factories, located at the southern end of the tunnel, are supported by a single BES batching plant equipped with two high-performance planetary mixers. The plant was engineered to operate efficiently within the site’s constraints, requiring installation between existing factory structures. To meet project requirements, advanced heated aggregate and water systems were included, ensuring consistent mix temperatures critical to the concrete specifications.
Designed to produce high volumes of concrete while maintaining stringent quality standards, each mixer functions independently to ensure uninterrupted operation even during maintenance. Integrated moisture and temperature measurement systems guarantee consistency across all batches.
Beyond concrete production, BES implemented a concrete reclaiming and water-management system featuring fiber-separation equipment and a filtration process. Wastewater was treated and processed through a CO2 pH correction system, ensuring any discharged water was clean and environmentally compliant.
In addition to the tunnel segment batching plant, BES installed two large bespoke concrete batching plants at the South Portal, where the tunnel works commence. These high-performance plants were designed to meet the project's extensive concrete demands and featured the same advanced heated aggregate and water systems for seamless integration and operational flexibility.
With extensive planning and expertise in bespoke concrete plant solutions, BES tailored the system to meet the unique challenges of the project, including environmental considerations, raw material transport logistics, and the need for specialised concrete mixes.
Through its innovative approach and technical expertise, BES successfully delivered, installed, and commissioned the batching plants, ensuring a reliable supply of high-quality concrete essential to the Chiltern Tunnel’s construction.
Working closely with project engineers, BES developed a dedicated twin-mixer concrete batching plant to supply two on-site precast tunnel segment factories. These factories produce high-performance steel-fiber-reinforced concrete (SFRC) segments, integral to the tunnel’s structure. With a total of 112,000 wall segments required, precision and consistency were paramount.
The two tunnel segment factories, located at the southern end of the tunnel, are supported by a single BES batching plant equipped with two high-performance planetary mixers. The plant was engineered to operate efficiently within the site’s constraints, requiring installation between existing factory structures. To meet project requirements, advanced heated aggregate and water systems were included, ensuring consistent mix temperatures critical to the concrete specifications.
Designed to produce high volumes of concrete while maintaining stringent quality standards, each mixer functions independently to ensure uninterrupted operation even during maintenance. Integrated moisture and temperature measurement systems guarantee consistency across all batches.
Beyond concrete production, BES implemented a concrete reclaiming and water-management system featuring fiber-separation equipment and a filtration process. Wastewater was treated and processed through a CO2 pH correction system, ensuring any discharged water was clean and environmentally compliant.
In addition to the tunnel segment batching plant, BES installed two large bespoke concrete batching plants at the South Portal, where the tunnel works commence. These high-performance plants were designed to meet the project's extensive concrete demands and featured the same advanced heated aggregate and water systems for seamless integration and operational flexibility.
With extensive planning and expertise in bespoke concrete plant solutions, BES tailored the system to meet the unique challenges of the project, including environmental considerations, raw material transport logistics, and the need for specialised concrete mixes.
Through its innovative approach and technical expertise, BES successfully delivered, installed, and commissioned the batching plants, ensuring a reliable supply of high-quality concrete essential to the Chiltern Tunnel’s construction.
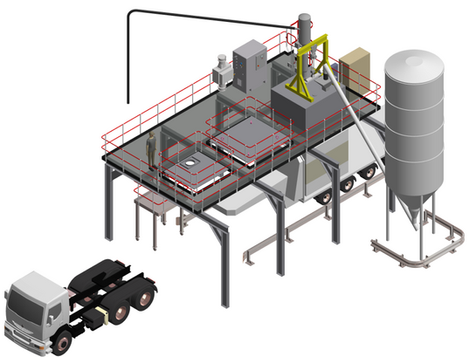
Magnox – Hinkley Point A
As part of Hinkley Point A site decommissioning works, there was a requirement to encapsulate legacy intermediate level radioactive waste, sand and sludge in 6m3 Reinforced Concrete Boxes.
Bower Engineering Solutions were tasked with producing concept design deliverables for an external grout mixing facility.
Works included:
• Producing 3D models and layout drawings of the new facility
• Production of sequence diagrams, flow diagrams
• Underpinning trial works which involved grout mixing and curing trials.
• Design, manufacture and test of:
• A bespoke single shaft grout mixing rig
• A 6m3 RCB mock-up
• Temperature monitoring and analysis systems
• Simulated materials
Bower Engineering Solutions were tasked with producing concept design deliverables for an external grout mixing facility.
Works included:
• Producing 3D models and layout drawings of the new facility
• Production of sequence diagrams, flow diagrams
• Underpinning trial works which involved grout mixing and curing trials.
• Design, manufacture and test of:
• A bespoke single shaft grout mixing rig
• A 6m3 RCB mock-up
• Temperature monitoring and analysis systems
• Simulated materials
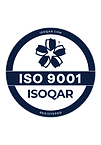

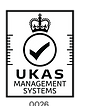

Need Help?
For any inquiries, questions or commendations, please call:
Tel: +44 (0) 1955 601 212
Email: info@berk-eng.com

bottom of page